Preliminary Hazard Analysis (PHA) Utility to Determine Equipment and Instrument Re-qualification Frequency
An Introduction to Equipment Qualification
The pharmaceutical industry induces full of experiments and it often requires conducting batch reactions using toxic or flammable materials. In many cases, complex chemical reactions are carried out with significant energy release. Such exothermic reactions processing can cause fire, explosion or runaway reaction hazards and these are quite life threatening for personnel and facilities. Equipment qualification is a critical step in overall process validation (PV), typically referred to as Stage 2A of the PV life cycle. It is outlined in many regulation and guidelines, including the FDA’s 2011 Process Validation Guidance and Annex 15 of the EU GMP, among others.
While handling the Equipment, one is likely to face the ambiguity of how often to do a given task or activity using them. It is necessary for the equipment to be periodically re-qualified if there is a performance dip with consistent working to ensure the quality of products. Here the focus is on the re-qualification decision-making framework based on the use of the preliminary hazard analysis (PHA), a tool used in quality risk management.
Prior to use in production or quality control testing all new equipment should require passing through all stages of qualification such as
- Design qualification (DQ)
- Installation qualification (IQ)
- Operational qualification (OQ)
- Performance qualification (PQ)
A robust equipment qualification program is appropriate based on the uses and risks of the equipment. The activities of each of these qualification steps should be well documented, to provide evidence that the equipment is fit for its intended purpose, and those records should be available for review by request.
Figure 1: Stages of equipment and instrument qualification
In the figure above, if we follow the illustration we see that once the equipment has been initially qualified, the qualification program should speak to the periodic re-qualification of equipment. It is a part of implementing any changes through a defined change control process impacting the qualified state of the equipment. Based on the criticality of the equipment used in production or on the quality control testing of products the extent of the re-qualification should be done. Documentation of the periodic review of pertinent data is indispensable to confirm that a process/method/system continues to consistently produce a result meeting predetermined acceptance criteria.
PRINCIPLES OF QUALITY RISK MANAGEMENT
Two primary principles of quality risk management in the pharmaceutical industry are:
- The risk evaluation of quality should be based on scientific knowledge and concern about the protection of the personnel and facilities.
- The quality risk management process should be commensurate with the level of risk with respect to the level of effort, formality, and documentation.
ICH Q9 on Preliminary Hazard Analysis (PHA)
As continuing to the question of “When or at what frequency should the periodic review is performed?” How should one structure the program to help the user determine when to perform the review? What guidelines to follow to create this aspect of the qualification program?
The answer to these is to perform the ICH Q9 (Quality Risk Management) – the risk management tool PHA. According to ICH Q9, the definition of PHA is that it is a tool to analyse hazardous situations and events that might cause harm, to estimate probable hazards in occurrence for a given activity, facility, product or system based on applying prior experience or knowledge of a hazard or failure to identify future hazards.
The tool consists of the following components:
- identification of the possibilities that the risk event happens
- qualitative evaluation of the extent of possible injury or damage to health as an outcome
- using a combination of severity and likelihood of occurrence, relative ranking of the hazard is given
- the detection of the possible remedial measures
Figure 2 denotes the PHA worksheet. If we can build a worksheet to organize the analysis and assist with the facilitation of the activities, the PHA tool could essentially address all the review of the parameters, as well as correlate the risk priority ranking to a periodic review frequency for the subject equipment.
It requires team expertise in the quality risk management process, how to use the PHA tool, scoring criteria, and key definitions. It generally consists of equipment owners, process owners, and quality assurance to perform the analysis possessing a strong understanding of the whole hazard analysis. The inputs of each column to the worksheet are directed and provided by a two-step triage approach using risk blocks scored against criteria as high, medium, and low rankings as in Tables 1, 2, and 3.
Figure 2: PHA worksheet example
Table 1: Severity Rankings
Table 2: Probability (Occurrence) Rankings
Table 3: Detectability Rankings
Figure 3: Risk class determination
The preliminary risk class based on severity and probability (or occurrence) was first determined as in Figure 3.
Figure 4: Risk priority ranking
Table 4: Example of Periodic Review Frequency
Further the hazard parameters are evaluated against detect-ability, resulting in a risk priority ranking (Figure 4). It correlates to the periodic review frequency for the subject equipment (Table 4). Once the worksheet is completed with input from team members, the periodic review frequencies should be reviewed and agreed to by all. The following PHA worksheet (Figure 5) provides an example of a completed analysis activity.
Figure 5: PHA worksheet example — completed analysis activity
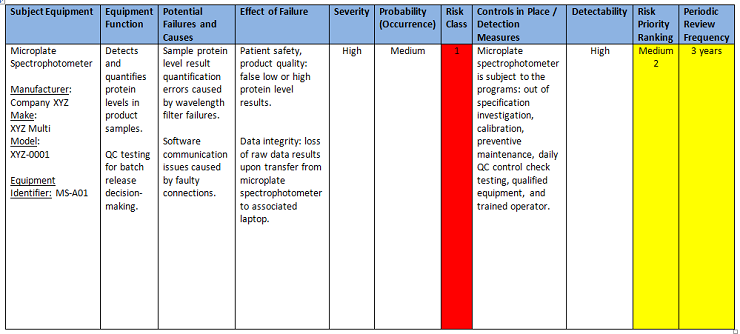
Inferences drawn about how this
method of hazard analysis can be beneficial
- The PHA tool enables to build a usable worksheet allowing all members of the team to participate in the risk analysis activity to provide subject matter expertise, voice concerns, and promote issues for further discussion.
- Additionally, by facilitating the team meetings, time schedules were managed and those issues that were a challenge were tabled and discussed offline.
- At the end of each completed worksheet, team members provide feedback regarding the risk analysis activity noting the efficient use of time, effective use of risk management tools, and delivery of risk priority rankings for subject equipment in correlation with the periodicity frequency.
- Therefore, using a risk management tool such as PHA, a periodic review frequency can be identified and applied to qualified equipment. This enables a timely recheck of the equipment by means of pertinent data like manufacturing performance trend data, change history, and/or deviation history and that in turn would help in assuring consistent production results meeting the predetermined acceptance criteria.