Autoclave Sterilization: Autoclaves provide a physical method for disinfection and sterilization. They work with a combination of steam, pressure and time. Autoclaves operate at high temperature and pressure in order to kill microorganisms and spores.
Autoclave Sterilization
Autoclave Sterilizers are used to decontaminate certain biological waste and sterilize media, instruments and lab ware. Regulated medical waste that might contain bacteria, viruses and other biological material are recommended to be inactivated by autoclaving before disposal.
An autoclave is used to sterilize surgical equipment, laboratory instruments, pharmaceutical items, and other materials. It can sterilize solids, liquids, hollows, and instruments of various shapes and sizes. Autoclaves vary in size, shape and functionality. A very basic autoclave is similar to a pressure cooker; both use the power of steam to kill bacteria, spores and germs resistant to boiling water and powerful detergents.
Do you want to do CANADIAN Masters Degree & Ph.D in Pharmacy under Canadian Universities
Autoclave Sterilizers:
To be effective against spore forming bacteria and viruses, autoclaves need to have steam in direct contact with the material being sterilized (i.e. loading of items is very important).
Create vacuum in order to displace all the air initially present in the autoclave and replacing it with steam.
Implement a well designed control scheme for steam evacuation and cooling so that the load does not perish.
The efficiency of the sterilization process depends on two major factors. One of them is the thermal death time, i.e. the time microbes must be exposed to at a particular temperature before they are all dead. The second factor is the thermal death point or temperature at which all microbes in a sample are killed.
The steam and pressure ensure sufficient heat is transferred into the organism to kill them. A series of negative pressure pulses are used to vacuum all possible air pockets, while steam penetration is maximized by application of a succession of positive pulses
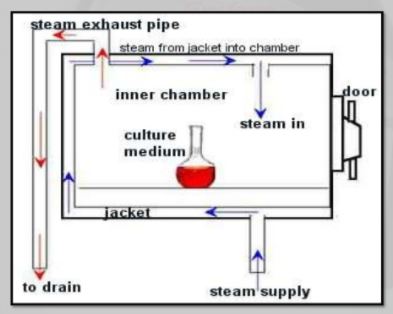
Autoclave Uses & Advantages:
An autoclave chamber sterilizes medical or laboratory instruments by heating them above boiling point. Most clinics have tabletop autoclaves, similar in size to microwave ovens. Hospitals use large autoclaves, also called horizontal autoclaves. They’re usually located in the the Central Sterile Services Department CSSD) and can process numerous surgical instruments in a single sterilization cycle, meeting the ongoing demand for sterile equipment in operating rooms and emergency wards.
They are important in tattoo shops, beauty and barber shops, dentist offices, veterinarians and many other fields.
Autoclave disadvantages:
Autoclave is unsuitable for heat sensitive objects.
Autoclaves Working Principle:
Autoclaves use pressurized steam as their sterilization agent. The basic concept of an autoclave is to have each item sterilized -whether it is a liquid, plastic ware, or glassware- come in direct contact with steam at a specific temperature and pressure for a specific amount of time. Time, steam, temperature, and pressure are the four main parameters required for a successful sterilization using an autoclave.
The amount of time and temperature required for sterilization depends on the type of material being autoclaved. Using higher temperatures for sterilization requires shorter times. The most common temperatures used are 121 C and 132 C. In order for steam to reach these high temperatures, steam has to be pumped into the chamber at a pressure higher than normal atmospheric pressure.
Now that we have covered the basic principle of how autoclaves use pressurized steam to sterilize contaminated materials, we will now go over how autoclaves operate.
Autoclave Design Diagram & Parts
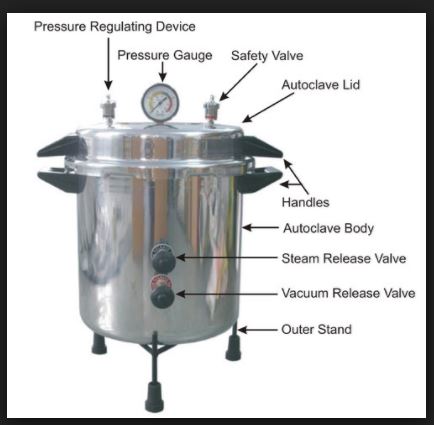
Similar to pressure cookers, steam sterilizer autoclaves work quickly and effectively because of their high temperature. The machine’s temperature and unique shape make it easier to hold the heat inside much longer. The autoclave also does a great job of efficiently penetrating each piece of equipment. The autoclave’s chambers are usually in the shape of a cylinder because cylindrical shapes are more equipped to handle the high pressure that is needed for the sterilization process to work. For safety reasons, there is an outside lock and a safety valve that prevents the autoclave steam sterilizer’s pressure from getting too high.
Once you close the autoclave sterilizer chamber, a vacuum pump removes all the air from inside the device or it is forced out by pumping in steam. If done the first way, the sterilizer is pumped with high pressured steam to quickly raise the internal temperature. On every autoclave there is a thermometer that is waiting for the thermal sweet point, 268-273 degrees Fahrenheit, and then it starts its timer. During the sterilizing process, steam is continuously entering the autoclave to thoroughly kill all dangerous microorganisms. Once the required time of sterilization has the elapsed, the chamber will be exhausted of pressure and steam allowing the door to open for cooling and drying of the contents.
Mode of Action Autoclave Sterilizers:
Moist heat destroys microorganisms by the irreversible coagulation and denaturation of enzymes and structural proteins. In support of this fact, it has been found that the presence of moisture significantly affects the coagulation temperature of proteins and the temperature at which microorganisms are destroyed.
Autoclave Working – Operation:
Place containers in the autoclave.
Check the strainer to see if it is clogged. The strainer is located on the bottom of the chamber near the door. The autoclave will not come up to pressure if the strainer is clogged.
Close door.
For the SMALL autoclave, rotate the handle clockwise until it is snugly closed.
For the LARGE autoclave, rotate the small, inner handle clockwise first until it locks. Then rotate the large outer handle clockwise until it is snug.
Open the glass-faced door in the upper right corner. Set STERILIZE time and, if needed, set DRY time.
Select the SETTING you want by pushing in the colored button that corresponds to:
ON-OFF FAST EXHAUST FLUIDS DRY
GREEN= FAST EXHAUST: Pressure will decrease rapidly at the end of sterilization. Fluids will bubble over if you use this setting.
YELLOW= Fluids: Pressure decreases more slowly at the end of sterilization.
BLUE=Dry: Use this setting for paper goods, cotton swabs, etc.
Push in the RED button to turn the autoclave on.
Wait until the temperature reaches 121°C and the RED sterilization light in the glass-faced box turns on before recording the Chamber Pressure on the Log. The chamber pressure should be 16-20 psi once the sterilization cycle starts. Anything below 16 psi should be reported to your lab manager.
At the end of the run, insure the CHAMBER PRESSURE has returned to ZERO before attempting to open the door. The FLUIDS cycle takes much longer than FAST EXHAUST – be patient. If the door cannot be easily opened, WAIT 10 minutes before trying again. If you wrench on the door and attempt to force it open, the internal metal rod that connects to the door handle will twist from the pressure.
To open the door:
SMALL autoclave: rotate the handle counterclockwise. Be careful, steam burns! Step to the side and crack open the door. Allow the steam to escape from the chamber then open the door and remove your items.
LARGE autoclave: First rotate the LARGE OUTER handle counterclockwise until it is loose. Next, rotate the SMALL INNER handle counterclockwise until the door opens. Be careful, steam burns! Step to the side and crack open the door. Allow the steam to escape from the chamber then open the door and remove your items.
As a courtesy to others needing to use the autoclave, promptly remove your items when the cycle is completed and you can easily open the door. Wear protective, heat resistant gloves when removing items.
Autoclaved waste materials are to be taken directly to the dumpster for disposal. Orange autoclave bags must be put into black trash bags before disposing in the dumpster.
Autoclave Cycles
To be effective, the autoclave must reach and maintain a temperature of 121° C for at least 30 minutes by using saturated steam under at least 15 psi of pressure. Increased cycle time may be necessary depending upon the make-up and volume of the load.
The rate of exhaust will depend upon the nature of the load. Dry material can be treated in a fast exhaust cycle, while liquids and biological waste require slow exhaust to prevent boiling over of super-heated liquids.
Liquids cycle
Liquids rely on the Liquids Cycle to avoid a phenomenon known as “boil-over.” Boil-over is simply a liquid boiling so violently that it spills over the top of its container. Boil-over will occur if the pressure in your autoclave chamber is released too quickly during the exhaust phase of the cycle. Significant liquid volume can be lost to boil-over, and this can result in unwanted spills on the bottom of the autoclave chamber that must be cleaned up to avoid clogging the drain lines and the subsequent repair costs to the department.
To help prevent boil-over during the exhaust phase, the chamber pressure must be released slowly. This process is controlled by the sterilizer’s control system. Controlling the exhaust rate allows the liquid load to cool off as the surrounding chamber pressure is decreased.
The exhaust rate for a Liquids Cycle is different from a standard Gravity or Vacuum Cycle, where the chamber pressure is released quickly. To prevent boil-over, the chamber pressure must decrease slowly to allow the temperature of the load to remain below the boiling point. If the pressure is exhausted all at once, the temperature of the load will be above its boiling point, resulting in instant and violent boiling.
(Slow Exhaust)
Material Recommended for:
Use with glass containers with vented closures; 2/3 full only
Solids or Dry cycle
(Fast Exhaust)
Material Recommended for:
Glassware: empty and inverted
no tight or impermeable closures
Dry hard items, either unwrapped or in porous wrap
Metal items with porous parts
Other porous materials
Gravity Cycle: Wrapped Goods or Pre vacuum cycle
(Clean: Fast Exhaust
Dirty: Slow Exhaust)
The traditional “Gravity Cycle” is the most common and simplest steam sterilization cycle. During a Gravity Cycle, steam is pumped into a chamber containing ambient air. Because steam has a lower density than air, it rises to the top of the chamber and eventually displaces all the air. As steam fills the chamber, the air is forced out through a drain vent. By pushing the air out, the steam is able to directly contact the load and begin to sterilize it.
At the end of the cycle, the steam is discharged through the drain vent. However, the load can still be hot and possibly wet. To address this issue, gravity autoclaves can be equipped with a post-cycle vacuum feature to assist in drying the load. The sterilizer runs a normal Gravity Cycle and after the load is sterilized, a vacuum pulls steam and condensation through the drain vent. The longer the vacuum system runs during the dry phase, the cooler and dryer the goods will be when removed from the chamber.
Gravity Cycles are commonly used on loads like glassware, bio-hazardous waste (autoclave bag waste), and wrapped and unwrapped instruments.
Material Recommended for:
Glassware that must be sterilized upright and/or can trap air
Wrapped dry items that can trap air
Pipette tip boxes
Sharps decontamination
(in collection containers)
Biohazard waste decontamination, in autoclave bags; can be wet or dry
Autoclave Types & Market
- Medical autoclaves
- Dental autoclaves
- Laboratory autoclaves
Medical autoclaves
Tabletop autoclaves
large horizontal autoclaves
Plasma Sterilizer
Washer Disinfectors
Autoclaves maintain a healthy, clean and sterile environment.
Fast and effective disinfection of surgical instruments in preparation for sterilization is ensured by Autoclaves.
Autoclaves that satisfy the needs of any hospital operating room, central sterile services department or medical clinic.
Dental autoclaves
– ideal sterilizer for dentists
Laboratory autoclaves
vertical loading autoclaves and fast liquid cooling autoclaves
Life science labs and research institutes need sterilization techniques inevitably
Autoclave Validation
Chemical Indicators
Tape Indicators
Tape indicators are adhesive-backed paper tape with heat sensitive, chemical indicator markings. Tape indicators change color or display diagonal stripes, the words “sterile” or “autoclaved” when exposed to temperatures of 121°C. Tape indicators are typically placed on the exterior of the waste load. If the temperature sensitive tape does not indicate that a temperature of at least 121°C was reached during the sterilization process, the load is not considered decontaminated. If tape indicators fail on two consecutive loads, notify your Department Safety Manager.
Tape indicators are not designed nor intended to prove that organisms have actually been killed. They indicate that a temperature of 121°C has been achieved within the autoclave. EHS recommends that you DO NOT use autoclave tape as the only indicator of decontamination or sterilization.
Integrated Chemical Indicator Strips
Integrated chemical indicator strips provide a limited validation of temperature and time by displaying a color change after exposure to normal autoclave operating temperatures of 121ºC for several minutes. Chemical color change indicators can be placed within the waste load. If the chemical indicators fail on two consecutive loads, notify your Department Safety Manager.
Biological Indicators
Biological indicator vials contain spores from B. stearothermophilus, a microorganism that is inactivated when exposed to 121.1oC saturated steam for a minimum of 20 minutes. Autoclaves used to treat biological waste will be evaluated with a biological indicator by EHS on a quarterly basis.
Validation Procedure for Autoclave:
EHS will coordinate biological validation testing with laboratory staff.
The indicators will be incubated by EHS for 24 hours at 60°C with a control that has been maintained at room temperature.
Results
If the autoclaved indicator exhibits growth, the validation has failed and will be repeated.
If the second validation indicator fails, EHS will notify the Department Safety Manager and request service on the autoclave. Autoclave should not be used until service has been conducted and the validation test passes.
Validation tests results are emailed by EHS staff to the appropriate labs and the Department Safety Manager.
EHS maintains documentation of all validation tests.
Autoclave Principle , Principle Of Autoclave , Working Principle Of Autoclave , Autoclave Principle Of Operation , Working Ggg Principle Of Autoclave , Autoclave Working Principle , Autoclave Principle And Working , Autoclaving Principle , Application Of Autoclave , Autoclave Working , Autoclave Principle Of Operation , Working Of Autoclave , Autoclave Application, Principle Of Autoclave Sterilization, Working Principle Of Autoclave , Working Principle Of Autoclave , Autoclave Principle And Procedure, Autoclave Working Principle, Autoclave Principle And Working,